A safe workplace is a tested and tagged workplace!
It’s important for your workers to be safe at work so they can return home to their families each and every day.
As an employer by law you must provide a safe place for your people to work and this must be done so in accordance with workcover and AS/NZS 3760:2010. This standard refers to in-service safety inspecting and testing of electrical equipment.
If you do not adhere to these standards your workplace will have to close its doors.
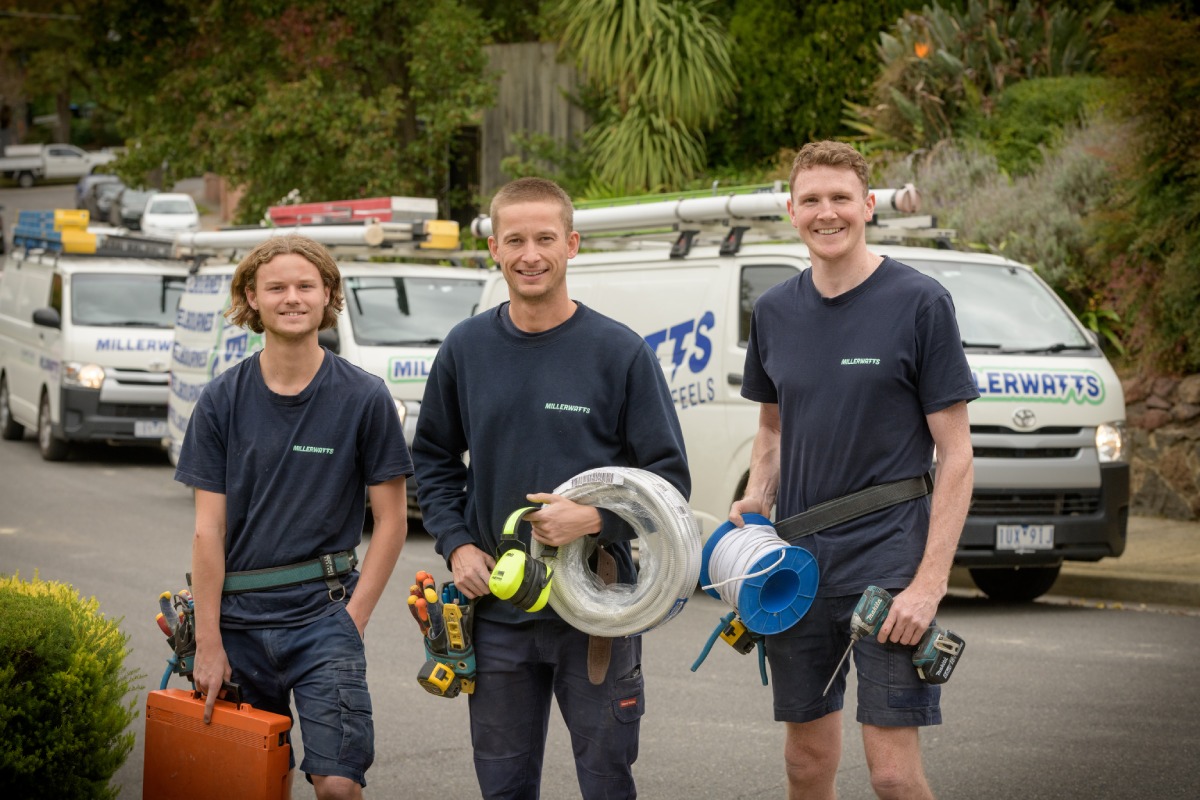
All businesses in the South Yarra area and surrounding suburbs must comply to these standards with testing and tagging of all electrical equipment and appliances being undertaken by a licensed electrician every 6 months for all manufacturing and workshop classified businesses.
All other businesses are only required to complete testing and tagging once per year to ensure they comply with the Australian standards.
In simple terms, any item that is plugged into a wall socket, socket board, or generator must be tested and tagged to achieve compliance. This includes everyday use items such as laptop and phone chargers, lighting, tools, fridges, and printers.
Whilst each electrical item must be tested and tagged you need to note the environment it is operating in to dictate how often it should be tested and tagged. This can be anywhere between 3, 6, or 12 months.
It is also critical that you keep a log of any new items that you may have purchased between now and the last routine test and tag you had conducted at your place of business. These items do not need to be tested and tagged immediately and can wait until your next routine test and tag, however, they must not be missed.
Millerwatts encourages our clients to keep a log of new items that require testing and tagging so they can be easily identified at the time or service and will not be missed and jeopardising compliance.
The Millerwatts test and tag service is available to Prahran business’ and is a comprehensive 5 step process.
Step 1. Visual inspection
Each item is visually inspected by a qualified electrician from Millerwatts. Any visible faults are recorded and identified to the business owner. The Millerwatts team generally finds that a high percentage of faults are found through visual inspection.
Step 2. Electrical inspection
Using the Millerwatts portable appliance tester your electrical goods are tested in line with Australian standards. Each item is individually tested to ensure a steady current, no surging or fluctuating current take-up.
Step 3. Appliance tagging
Once the items have been visually inspected and electrically tested they are then tagged with a pass or fail tag. Only items that are tagged with a pass tag can be continued to be used within the business.
Step 4. Reporting
Each business is required to upkeep an asset register for each individual item as well as a pass and fail report. At the completion of the inspection and testing the pass and fail report is emailed to the business operator for record-keeping.
Step 5. Scheduling
To ensure you and your business uphold your compliance requirements our servicemen will work with you to reschedule your test and tag services in line with your obligation or either 3,6 or 12 months depending on your business environment.
If you are unsure of your duty of care when it comes to testing and tagging or you just have a few questions, contact our team today. Our team can provide obligation-free quotes over the phone and answer all of your questions no matter how big or small.